SOFTWARE AND TOOLS
The SS 9000 Software Suite is designed to run static, semi-static and fatigue tests both with single-axis and multi-axes systems.
The software is compatible with all RTC 9000 controllers and with all software tools developed by LiTem.
PROFILE EDITOR Tool is an additional component of the SS 9000 software suite which allows variable profile, cyclical fatigue tests to be performed. It is essential when the replication is required for variable profile load curves, arising from in-field acquisitions or from user defined ones.
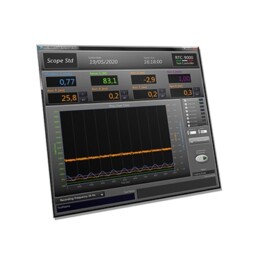
Software Tool SCOPE
The software tool SCOPE activates the reading mode of 4 analogue channels of the RTC 9000 and RTC 9001 controllers. The tool allows to display and record the acquired values by the additional channels in a synchronised way with the test values of channel 1 of the controller.
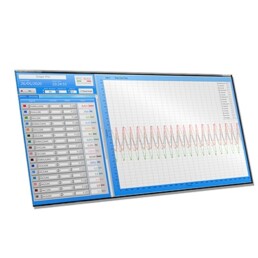
Software Tool SCOPE PRO
The software tool SCOPE PRO activates the reading mode of 4 analogue channels of the RTC 9000 and RTC 9001 controllers. The tool allows to display and record the acquired values by the additional channels in a synchronised way with the test values of all channels (up to 4 axes) of the controller. The operator can set the inputs to be displayed and recorded.
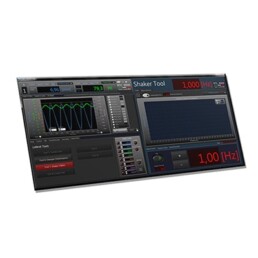
Software Tool SHAKER
The software tool SHAKER is used for tests on vibrating tables or shakers. Tests can be run with frequency set in manual or automatic mode and tests with frequency sweep with constant acceleration.
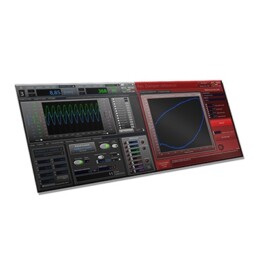
Software Tool DAMPER
The software tool DAMPER allows the operator to run tests on any kind of shock absorber. The operator can set reference curves and monitor the actual performance of the shock absorber. This is ideal for quality checks during production and in maintenance and assistance phases.
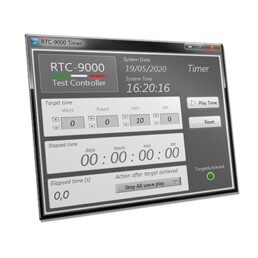
Software Tool TIME
The software tool TIME allow to set the duration of the fatigue test, using time definition instead of number of cycles. The test is interrupted when the set time has elapsed.